Introduction
When selecting the right hardware for mechanical and manufacturing applications, one decision you’ll need to make is whether to use a flange nut or a nut and washer combo. While both can securely fasten parts together, there are some key differences to consider before making your choice.
In this guide, we’ll dig into the pros and cons of each option so you can determine which is the better fit for your specific project. We’ll cover topics like:
- What are flange nuts and nut and washer combos?
- Main differences between the two options
- Pros and cons of each fastener type
- Ideal applications and uses for each
- How to select the right size and material
- Flange nut vs. nut and washer pricing
By the end, you’ll have a clear understanding of how flange nuts and nut and washer combinations differ and when one may be better suited than the other. Let’s get started!
What Are Flange Nuts and Nut and Washer Combos?
First, let’s review what exactly flange nuts and nut and washer combinations are:
Flange Nut
A flange nut is a type of locknut with an integrated flange (or collar) built around the base. The flange provides a bearing surface that exerts pressure against the application surface when the nut is tightened. This creates added holding power to prevent loosening.
The flange also acts as a washer, eliminating the need for a separate external washer in many applications. Flange nuts are commonly available in steel, stainless steel, and brass.
Nut and Washer
As the name suggests, this fastener combo simply consists of a standard hex nut paired with a washer. The two separate pieces work together to evenly distribute load, reduce wear, and help prevent loosening.
Washers are typically available in steel, stainless steel, and other metal alloys. Nuts come in a wide variety of thread sizes, materials, and designs, like hex nuts, coupling nuts, lock nuts, and more.
Main Differences Between Flange Nuts and Nut/Washer Combos
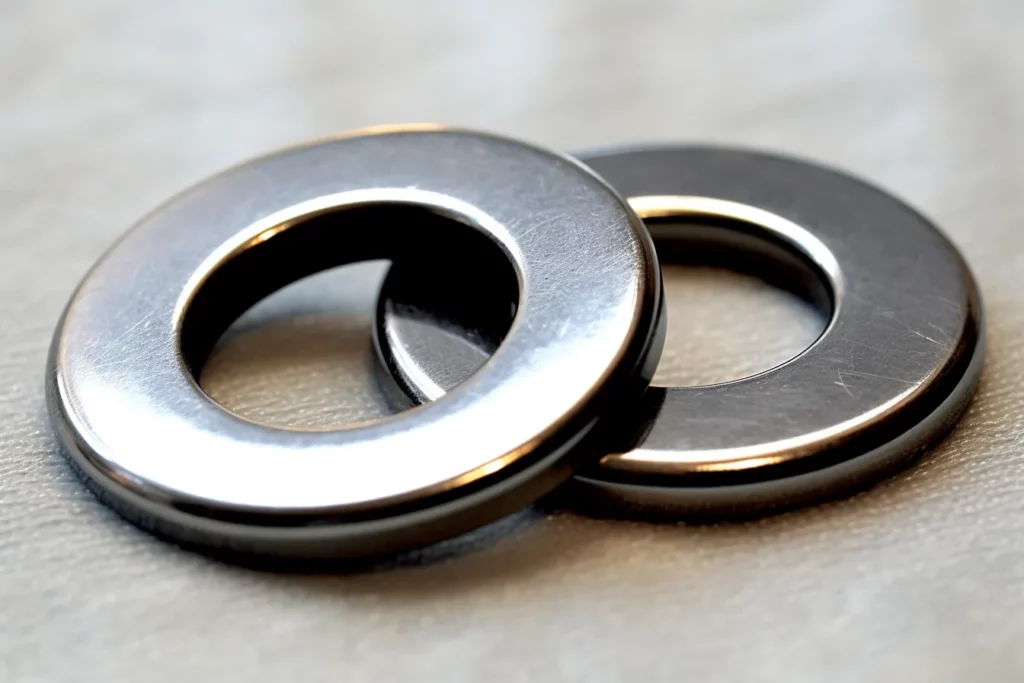
Now that we’ve defined both options, let’s look at some of the key differences between flange nuts and nut and washer combinations:
- Integrated vs. separate components – The main difference is that a flange nut combines the fastening nut and washer into one single component, whereas the nut and washer are two separate pieces.
- Locking ability – Flange nuts have greater holding power and resistance to vibration and loosening. The flange/collar design creates additional friction and locking action.
- Assembly – Flange nuts are faster and easier to install as a single component. Nut and washer combos require handling two separate pieces.
- Weight – Flange nuts are typically lighter than a nut and washer combo. Less material is used to construct the integrated flange design.
- Thickness – Flange nuts have a lower profile. Their slim integrated washer flange takes up less space than a separate standalone washer.
- Load distribution – Nut and washer combinations can distribute force over a larger surface area. The separate washer is wider than a flange collar.
As you can see, there are some clear trade-offs between the integrated convenience of flange nuts and the customizable strength of nut and washer combos.
Pros and Cons of Flange Nuts
Now that we’ve compared the two, let’s dive deeper into the specific pros and cons of flange nuts:
Pros:
- Single integrated component for faster assembly
- Locking flange design prevents vibration loosening
- Lighter weight than nut and washer combos
- Low profile/thickness for space-constrained applications
- Eliminates need for separate washers in many applications
- Wide material selection including steel, stainless steel, and brass
Cons:
- Limited flange thickness doesn’t distribute load over large area
- Not as customizable as mixing washer sizes and materials
- More expensive than regular hex nuts
- Requires flange nut-specific tooling for installation/removal
- Lack of lubrication can cause seizing/galling
Overall, flange nuts excel in high vibration applications where preventing loosening is critical, as well as weight-sensitive and space-constrained designs.
Pros and Cons of Nut and Washer Combos
For nut and washer combinations, here are some of their notable advantages and disadvantages:
Pros:
- Highly customizable mixing and matching washers and nuts
- Thicker washers can distribute load over larger surface
- Washer teeth/serrations can increase grip
- Reusable combination if low-cost standard hardware
- Easy to disassemble with standard wrenches
- Variety of nut styles beyond flange nut (hex, lock, etc.)
Cons:
- Two separate components to handle and assemble
- Potential for washers to get lost or left out
- Higher weight than flange nut option
- Loosening and vibration issues if not properly torqued
- Lack of integrated locking feature
- Potential need for threadlockers to prevent loosening
Overall, nut and washer combinations offer more flexibility and customization for specific applications. But they lack convenience and locking ability compared to single-piece flange nuts.
Ideal Applications and Uses
Now that we’ve weighed the pros and cons, here are some ideal uses for each fastener type:
Best Uses for Flange Nuts
Flange nuts excel in applications like:
- Securing bearings, pulleys, and other rotating parts
- Fastening components in high vibration environments
- Applications where a lower profile is needed
- Weight-sensitive designs like aircraft assemblies
- Anywhere resistance to loosening is critical
They work well with tapped holes and studs in materials like metals and plastics. The integrated flange replaces washers in many situations.
Best Uses for Nut and Washer Combos
Meanwhile, nut and washer combinations work best for:
- Applications requiring distribution of load over a larger area
- Fastener assemblies subject to frequent disassembly
- Locations where customizable washer size/material is beneficial
- Preventing wear and abrasion between parts
- Basic cost-sensitive assemblies with reusable hardware
- Securing objects to flat surfaces like walls or plates
They’re ideal when you need a versatile mix-and-match fastening solution. Separate washers also allow enhanced grip, positioning, and load spreading.
How to Select the Right Size and Material
When choosing either flange nuts or nut and washer combos, you’ll need to consider factors like:
- Thread size – Match the nut size to the tapped hole, stud, or machine screw. Standard sizes include M3, M4, M5, M6, 1/4”, 5/16”, 3/8”, etc.
- Nut thickness/height – Make sure it fits within the space constraints of the assembly. Flange nuts are lower profile.
- Flange OD/washer size – Diameter should allow adequate load distribution. Washer OD can be larger than flange OD.
- Hardness – Softer materials like brass are easier to tighten but won’t resist loosening. Steel resists vibration loosening.
- Coating – Zinc plating or wax coatings reduce corrosion and galling.
- Strength – Grade 5 and Grade 8 steel nuts offer more strength than lower grades.
- Material – Consider corrosion resistance, temperature ratings, strength requirements, and cost.
Proper nut and washer selection ensures a secure fit, sufficient strength, and optimal performance in the application. Don’t sacrifice quality to cut costs on critical fasteners.
Flange Nut vs. Nut and Washer Pricing
When evaluating the two options, hardware pricing is another factor to consider. Here’s an overview:
- Flange nuts – More expensive than regular hex nuts. Stainless steel and brass flange nuts can cost $5-$20 per nut depending on size.
- Nuts – Inexpensive basic hardware starting around $0.10-$2 per nut in steel and stainless. Higher costs for alloy and grade 8 nuts.
- Washers – Very low cost at $0.01 to $1 per washer in steel and stainless. Prices rise for specialty alloys and designs.
So while separate nut and washer combos keep costs down with basic hardware, the extra labor for assembly often makes flange nuts more economical overall for many automated and production applications.
Conclusion
Understanding when to choose a flange nut versus combining a nut with a washer enables selecting the best fastener for specific mechanical requirements. Keep these key tips in mind:
- Use flange nuts when you need vibration resistance, weight savings, and fast assembly. The integrated flange eliminates separate washers.
- Pick nut and washer combinations for customizability with mixing materials and sizes. Ideal for applications needing load distribution.
- Compare pros and cons to select the right option for your installation needs, cost constraints, and performance demands.
- Match nut size, material, coating, and strength ratings to your application. Don’t cut corners on critical fasteners.
For specialty applications, custom flange nuts or washers can also be manufactured. Consulting a fastener specialist is advised for unique requirements.
Contact Jmet Corp at +86 17768118580 or email [email protected] for any inquiries about flange nuts, nut and washer combos, or custom hardware for your project! Our engineering team is ready to help you find the ideal solution.
Links provided by Claude may not always be valid or up to date. We appreciate your patience as we work to improve link accuracy.CopyRetry