Introduction
Marine fasteners play a crucial role in the construction and maintenance of boats, ships, offshore structures, and other marine applications. These specialized fasteners are designed to withstand the harsh marine environment, including exposure to saltwater, humidity, UV light, and the risk of corrosion.
In this article, we will explore the importance of marine fasteners, discuss their corrosion resistance properties, and highlight different types of fasteners commonly used in the marine industry.
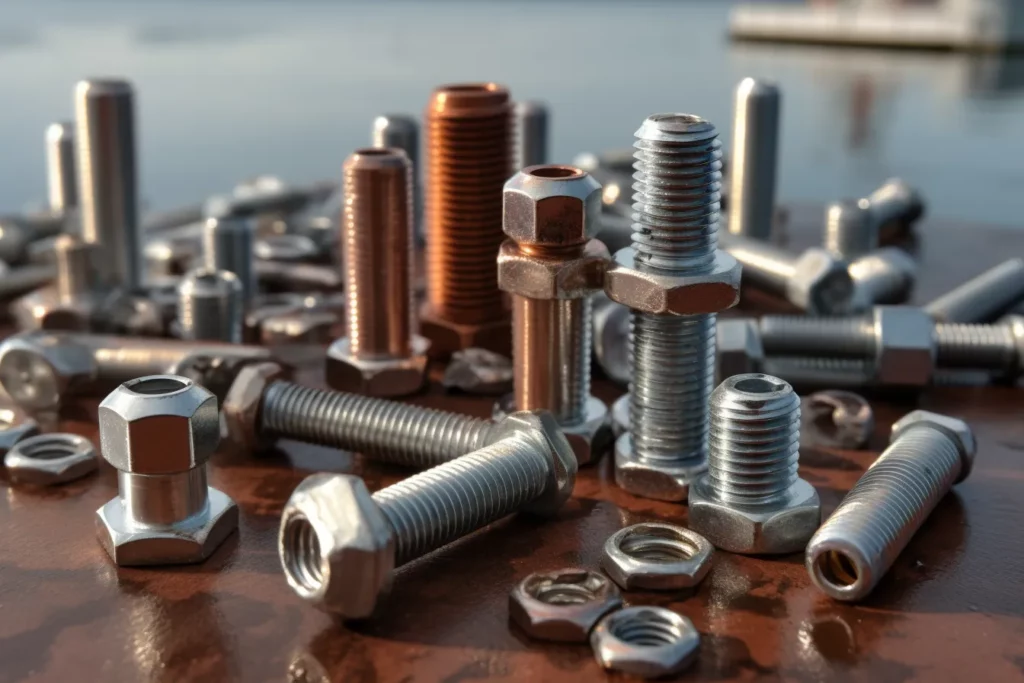
Importance of Marine Fasteners
The use of appropriate marine fasteners is essential for ensuring the safety and longevity of marine structures. The marine environment poses unique challenges such as the corrosive nature of saltwater and the constant exposure to moisture. Therefore, selecting the right fasteners is crucial to maintain the structural integrity and prevent potential failures.
Corrosion Resistance Properties
One of the key considerations when choosing marine fasteners is their corrosion resistance. Stainless steel fasteners, particularly those made of 316 stainless steel, are widely regarded as the best choice for marine applications due to their high corrosion resistance. Stainless steel fasteners are available in different grades, with higher numbers indicating higher corrosion resistance. For instance, 316 stainless steel offers more corrosion resistance compared to 304 stainless steel .
Types of Marine Fasteners
- Stainless Steel Fasteners: Stainless steel fasteners, such as screws, bolts, and nuts, are widely used in the marine industry. They offer excellent corrosion resistance and durability in marine environments. Common stainless steel grades used for marine fasteners include 18-8, 304, and 316 stainless steel.
- Silicon Bronze Fasteners: Silicon bronze fasteners are another popular choice for marine applications. They exhibit excellent resistance to corrosion, especially in saltwater environments. These fasteners are commonly used in boat building and other marine structures .
- Plastic Marine Fasteners: Plastic marine fasteners offer an alternative to metal fasteners. They are particularly useful in applications where corrosion is a concern. Plastic fasteners, such as nylon or polypropylene, do not rust and can provide adequate strength for non-critical marine components.
Installation and Maintenance
Proper installation and regular maintenance of marine fasteners are vital to ensure their effectiveness. It is important to follow the manufacturer’s guidelines for installation torque, use of anti-seize compounds, and proper sealing techniques. Additionally, periodic inspections and cleaning of fasteners can help prevent corrosion and maintain their performance over time.
Conclusion
Marine fasteners are essential components in the construction and maintenance of marine structures. They provide the necessary strength and corrosion resistance required to withstand the harsh marine environment. By selecting the appropriate materials, such as stainless steel or silicon bronze, and following proper installation and maintenance practices, one can ensure the safety, durability, and longevity of marine structures.
Remember to consult specific guidelines and standards recommended by experts in the field of marine fasteners to ensure the best practices for your specific application .