Introduction
The significance of quality inspection in fasteners for automotive components cannot be overstated. With the keyword “Quality Inspection of Fasteners for Automotive Components,” this article will delve into the importance of quality inspection, the techniques involved, and its impact on safety and reliability.
The Importance of Quality Inspection
- Ensuring Safety: Safety is paramount in the automotive industry, and fasteners play a critical role in maintaining the integrity of components. Through rigorous quality inspection, manufacturers can identify any defects or weaknesses in fasteners, ensuring they meet the required safety standards. By prioritizing safety, potential accidents and risks can be mitigated.
- Preventing Failures: A single faulty fastener can lead to catastrophic consequences, compromising the performance and safety of the vehicle. Quality inspection techniques, such as dimensional checks and mechanical testing, help identify potential issues early on. By detecting and addressing these problems, manufacturers can prevent failures and costly recalls, saving lives and resources.
- Enhancing Reliability: Automotive components must perform consistently under various operating conditions. Quality inspection processes, including visual inspection, dimensional checks, and torque testing, ensure that fasteners meet the required specifications. By maintaining high-quality standards, manufacturers can enhance the reliability of automotive components, reducing unexpected failures and improving customer satisfaction.
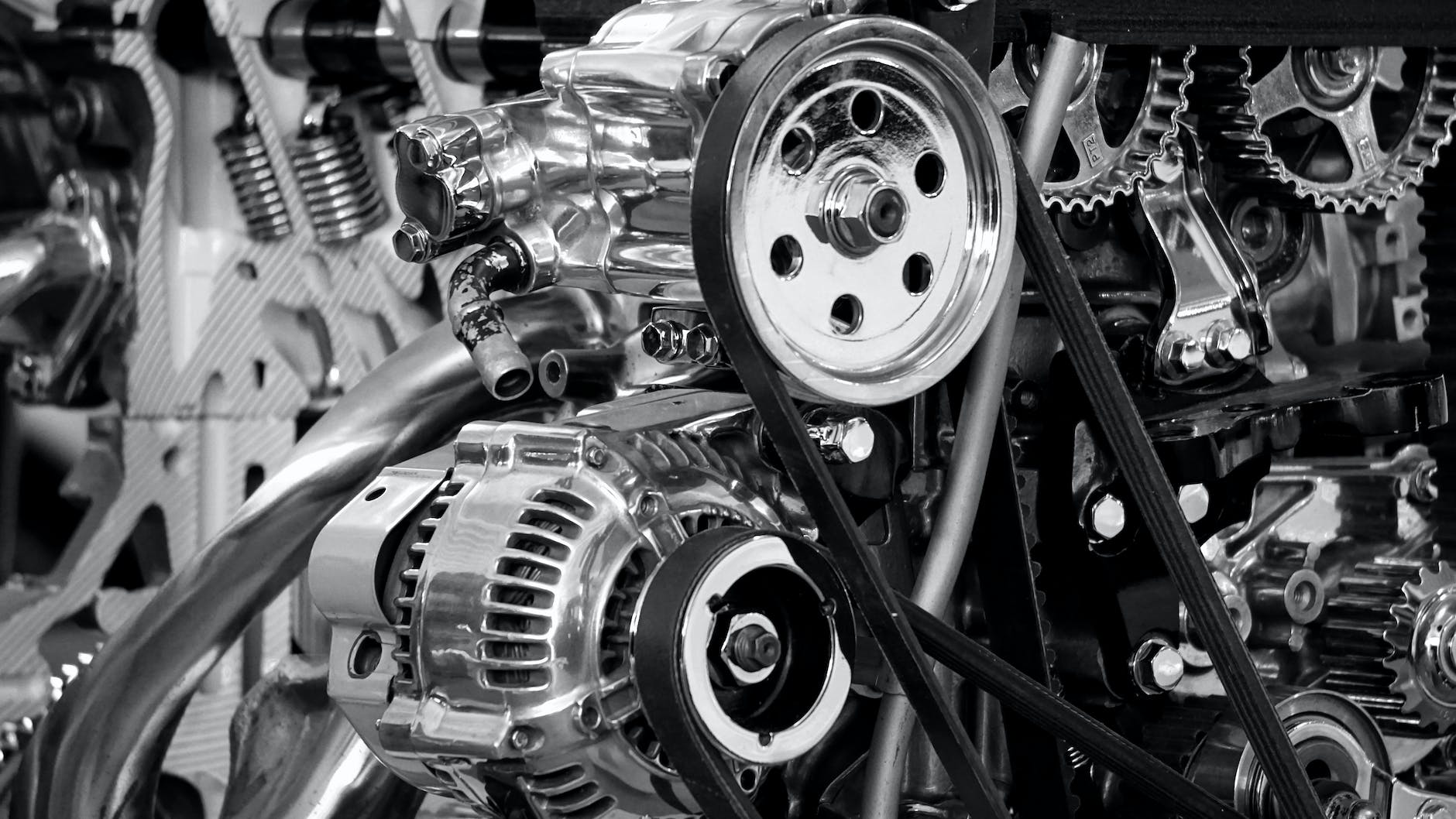
Quality Inspection Techniques
- Visual Inspection: Visual examination is an essential first step in quality inspection. Skilled inspectors carefully examine fasteners for any visible defects, such as cracks, dents, or deformities. Additionally, they check for proper coating and surface finish, as corrosion resistance is crucial in automotive applications.
- Dimensional Checks: Fasteners must adhere to specific dimensional requirements to ensure compatibility and proper fit. Through precise measurement tools, inspectors verify critical dimensions, including thread pitch, diameter, length, and head shape. By identifying non-conforming fasteners, manufacturers can maintain assembly integrity and prevent potential issues.
- Mechanical Testing: Fasteners need to withstand various loads and stresses during operation. Mechanical testing, such as tensile strength, yield strength, and hardness tests, evaluates the strength and performance of fasteners. This enables manufacturers to ensure that the fasteners can withstand the expected operating conditions and maintain their functionality over time.
- Torque Testing: Proper clamping force is essential for the reliable performance of fasteners. Torque testing involves measuring the torque applied during assembly to ensure it aligns with the specified requirements. By conducting torque tests, inspectors can identify fasteners that may fail or loosen under specified torque, enabling manufacturers to address any issues promptly.
- Thread Inspection: Threaded fasteners rely on accurate thread geometry for effective engagement and load distribution. Inspectors utilize thread gauges to check critical parameters such as thread pitch, flank angle, and root radius. By ensuring the quality and precision of threads, manufacturers can guarantee the fasteners’ ability to securely hold components together.
Statistical Process Control and Data Analysis
Manufacturers often implement statistical process control (SPC) techniques during fastener production to ensure consistent quality. SPC involves collecting and analyzing data at various stages of manufacturing to monitor the quality of fasteners. Data tables are used to track important quality parameters, such as dimensional tolerances, hardness values, and torque specifications.
Analyzing collected data enables manufacturers to identify trends, variations, and potential process deviations. By applying statistical methods, such as control charts and process capability analysis, proactive measures can be taken to maintain quality standards, minimize defects, and optimize production processes.
Conclusion
In conclusion, the quality inspection of fasteners for automotive components is paramount in ensuring safety and reliability. By employing various inspection techniques and utilizing statistical process control, manufacturers can identify defects, prevent failures, and enhance the overall quality of fasteners. Prioritizing quality inspection in the production process leads to safer vehicles, reduced risks, and improved customer satisfaction.